一、压铸模具基本结构
常用的压铸模具有两个半模组成,分别称为定模和动模。也有更复杂的压铸模具,不止两个半模。压铸模具的组成部分

如图1所示。

如图1所示。
压铸模具组成部分的作用如下:
(1) 直浇道 联通压室或至横浇道,包括浇口套和分流锥等。
(2) 浇注系统 合金液进入型腔的通道,包括内浇道、横浇道及直浇道等。
(3) 型腔 在镶块上形成,形成压铸件的几何形状。
(4) 抽芯机构 完成活动型芯的抽出及插入动作,包括滑道、滑
块、油缸、斜杠等。
(5) 排溢系统 排出气体及存储冷金属残渣等。
(6) 温度控制系统 控制压铸模具的温度,包括冷却水管和加热油管等。
(7) 顶出机构 将压铸件从型腔中顶出,包括顶杆等。
(8) 动模框 连接及固定动模部件,包括套板、支撑板等。
二、压铸模具的设计
设计压铸模具要注意以下几个要点:
(1)要尽可能地采用先进简单的结构,保证动作稳定可靠及日常维护、维修。
(2)要考虑浇注系统的可修改性,在调试过程中可以进行必要的修改。
(3)合理选用各种公差、缩尺及加工余量,保证可靠的模件配合及要求的压铸件精度。
(4)选用合适的模具材料和可靠的热处理工艺,确保压铸模具的使用寿命。
(5)应具有足够的刚度及强度,能够承受锁模压力和涨型力,压铸生产过程中不产生变形。
(6)尽可能使用标准化的压铸模具零件,改善经济性及互换性。
在设计模具的时候,还要根据铸件的投影面积计算出压铸生产时的总投影面积、压射比压,来选择合适吨位的压铸机,公式如下:
F涨型力=100 P压射比压×S投影面积
F锁模力=F涨型力/K系数
式中,K系数一般选取0.85。
压铸机选好以后,根据压铸机的动、静行板及压射偏心位置等尺寸,设计模具的大小、中心位置、复位拉杆孔位等与压铸机相连接部分的尺寸。
随着我国汽车制造业的发展,越来越多的汽车零部件采用了铝合金材质,例如汽车发动机的缸体、缸盖、油底壳以及各类连接支架等。随着压铸技术的日益成熟,各汽车厂商对压铸件的内部质量要求越来越高,尤其以德国大众的要求最为严格,每一种车型的发动机压铸件产品都有一套相应的技术要求,产品孔隙度的要求是每一种零部件所必须的要求。
一些零部件结构上非常复杂,需要在模具上做一些相应的结构才能实现批量压铸生产,例如零部件上有多种角度的螺纹孔,要保证加工后的产品质量,必须在模具的相应位置制作型芯,

如图2所示。

如图2所示。
图2中,A为定位孔,B是3个M8的螺纹孔,与定位孔呈10°角,其中右侧的两个螺纹孔是通孔;C是两个螺栓过孔,与定位孔呈5°角;D孔是与定位孔呈34°的螺纹孔,长度是38mm。
抽芯机构按驱动方式可分为机械式和液压式两种。机械式抽芯主要通过开合模过程中斜销、弯销、齿轮、齿条等实现抽芯与复位。液压抽芯机构的工作原理比较简单,直接利用液压缸进行抽芯及复位动作。液压抽芯机构可以根据抽芯力的大小及抽芯距离的长短选择液压缸的尺寸。图2产品在模具设计时首先考虑C、D三个孔要铸出来,可以分别用液压抽芯机构采取有角度的滑道的方式在生产中来实现孔的成形。图3是D孔的滑道机构示意,用这种办法可以将液压缸设计在模具外面,这样设计的好处是模具可以变薄,连续生产过程中便于维护。
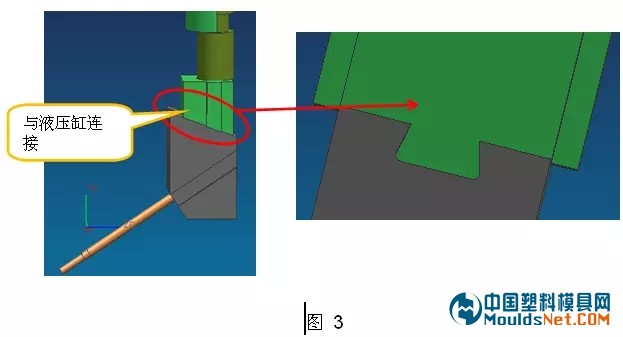
在连续生产过程中,模具的抽芯孔会因为多次的抽插滑动造成抽芯孔变形,在模具寿命的中后期,会经常出现抽芯研死的现象,为了解决这一问题,可以在抽芯孔的部位增加一个镶套,如果出现抽芯孔变形的情况,就可以更换镶套来解决(见图4)。这种办法也可以应用在模具的顶杆处,只要能加镶套的,就都可以做这个结构。

由于一些零部件图样的要求,铸件上一些区域需要放置规定大小的异形顶杆。圆圈内的4个顶杆成形部分(见图5)是阶梯形式的,直径为8mm。由于铸件动模型腔比较深,所以产生的抱紧力就很大,顶杆顶出铸件时所需要的力就大,顶杆在压铸生产过程中容易折断。由于铸件成形部分顶杆的直径由产品图样确定,可以根据产品的特点,设计阶梯粗细的顶杆,以保证顶杆的寿命。

由于有了C、D两个角度的油缸在模具上,B所示的3个M8的螺纹孔就没有位置再采用油缸的方式来做预铸孔了,两个M8螺纹通孔是18mm深,想保证内部质量必须做出预铸孔,我们采取了做对接异形型芯的方式来解决这个问题,对接的形式如图6所示。

型芯不是正常对接的,错开了一定的距离,在两型芯对接的部分是正常的出模斜度(一般设计在1°~1.5°之间,两个型芯的外侧的出模斜度就是正常的出模斜度外加与定位孔所呈的角度。
由于某些复杂的产品厚大区域通过压铸工艺参数是无法保证内部质量,所以在设计模具时要考虑增加局部挤压机构,这种机构的原理是在压射完成的最短时间内,将抽芯插入,使得这一区域压实,减少气孔。挤压机构抽芯的成形部分是没有出模斜度的,所以只适合短程的结构。
三、压铸工艺系统设计
模具大框设计好后,就进入了浇注系统的设计,早先都是看二维或三维图样根据实践经验来做这一部分的。在生产过程中根据产品的内部质量来调整内浇道的位置和方向。近十几年来,随着铸造充型凝固过程数值模拟技术的不断发展以及铸造行业的市场需求,铸造过程模拟商品化软件不断出现。很多主机厂也要求在设计模具前看到压铸模拟过程,因此很多模具厂家都使用了MAGMAsoft或ANYCASTING这两种模拟软件,在设计之初将设计好的三维导入到这个程序里面,设定压铸工艺参数后,模拟软件经过一定的运算来得出接近实际生产效果的模拟动画如图7~图10所示。



(a) (b)
图9 凝固模拟

压铸工艺要求模拟达到的效果如下:
(1) 合金液应或多或少地同时到达内浇道处。
(2) 在填充过程中合金液应平稳填充。
(3) 填充过程中不能出现卷气或紊流的效果。
(4) 填充完成前,合金液不能将集渣包过道封死。
(5) 从填充过程中所产生的冷金属不能存在铸件内,应全部被驱赶到集渣包里。
根据填充模拟和粒子追踪模拟,以及压铸工艺的要求,模具的浇道和集渣包的位置和大小都要做到相应的优化;根据凝固模拟和铸件的壁厚,模具内冷却水和加热油管,以及点冷却的的位置能够确定;根据模具冲蚀模拟可以确定模具的哪些地方需要重点喷涂。通过模拟分析,在设计时就解决了浇口和集渣包手动优化的过程,这样就节省了模具制造时凭经验所产生偏差造成的模具修改过程。
为了使铸件的质量得到进一步的提高,一些公司利用抽真空技术使废品率下降,创造更高的价值。日本的抽真空技术非常成熟,我国也借鉴了一些他们的经验。抽真空技术要求模具排气道的面积是冲头面积的1:100。在快压射开始前的0.4s启动真空泵,抽真空在设计模具时可以根据产品的复杂程度和模具的大小,来确定使用真空排气波板或真空阀的数量。图11是模具上抽真空的结构。
如果抽真空技术应用较好的情况下,铸件的废品率至少要降到原有废品率的20%以下。但由于抽真空设备价格很高,一些压铸厂只是将其用在废品率较高的产品模具上。